Zero-emission power boost to the tractor-trailer combination. Our interview with the founder of Trailer Dynamics
Trailer Dynamics has developed a comprehensive solution, also called e-kit, to equip the trailer with an electric drivetrain. This results in the possibility of driving the semitrailer-trailer system more efficiently and sustainably, as stated by the company. The e-axis, traction batteries, and real-time control unit are the key components of the e-kit. We met Michael W. Nimtsch, the founder of Trailer Dynamics, who told us more about the entire project.
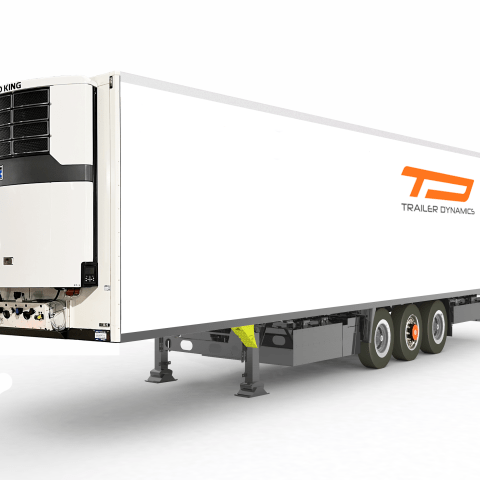
Technology innovators. This is how Michael W. Nimtsch, who founded Trailer Dynamics back in 2018, defines the company, which boosted a relevant and impressive booth at the last IAA Transportation in Hannover. Trailer Dynamics has developed a comprehensive solution, also called e-kit, to equip the trailer with an electric drivetrain. This results in the possibility of driving the semitrailer-trailer system more efficiently and sustainably, as stated by the company. The e-axis, traction batteries, and real-time control unit are the key components of the e-kit. The first may support the primary drive of the tractor unit throughout the entire journey and enables a constant reduction in the tractor unit’s fuel consumption.
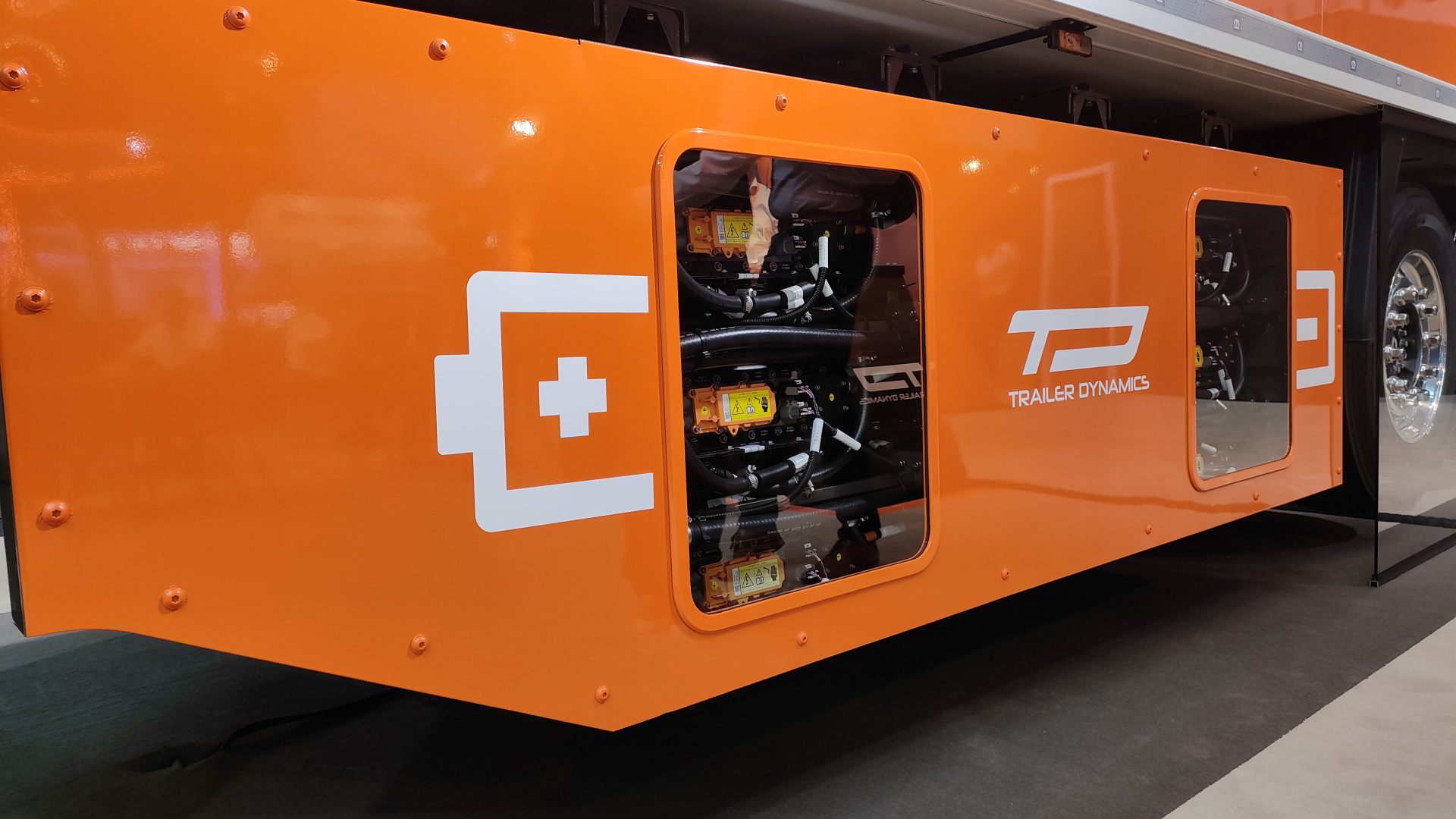
Trailer Dynamics: getting closer to pre-series
We met the founder of Trailer Dynamics. He confirmed that the company is getting closer to the market entrance. “In 2025 we’ll be ready with a pre-series, while full series is expected by 2026”. But there’s more.
Mr Nimtsch, how would you describe your company, Trailer Dynamics?
We’re technology innovators in the field of heavy-duty trucks, with a clear focus on trailers. We’re providing solutions in the field of decarbonization or increase of efficiency. In our trailers, the middle axle of the three axles is electrified by means of two powerful motors with 345 kW per motor.
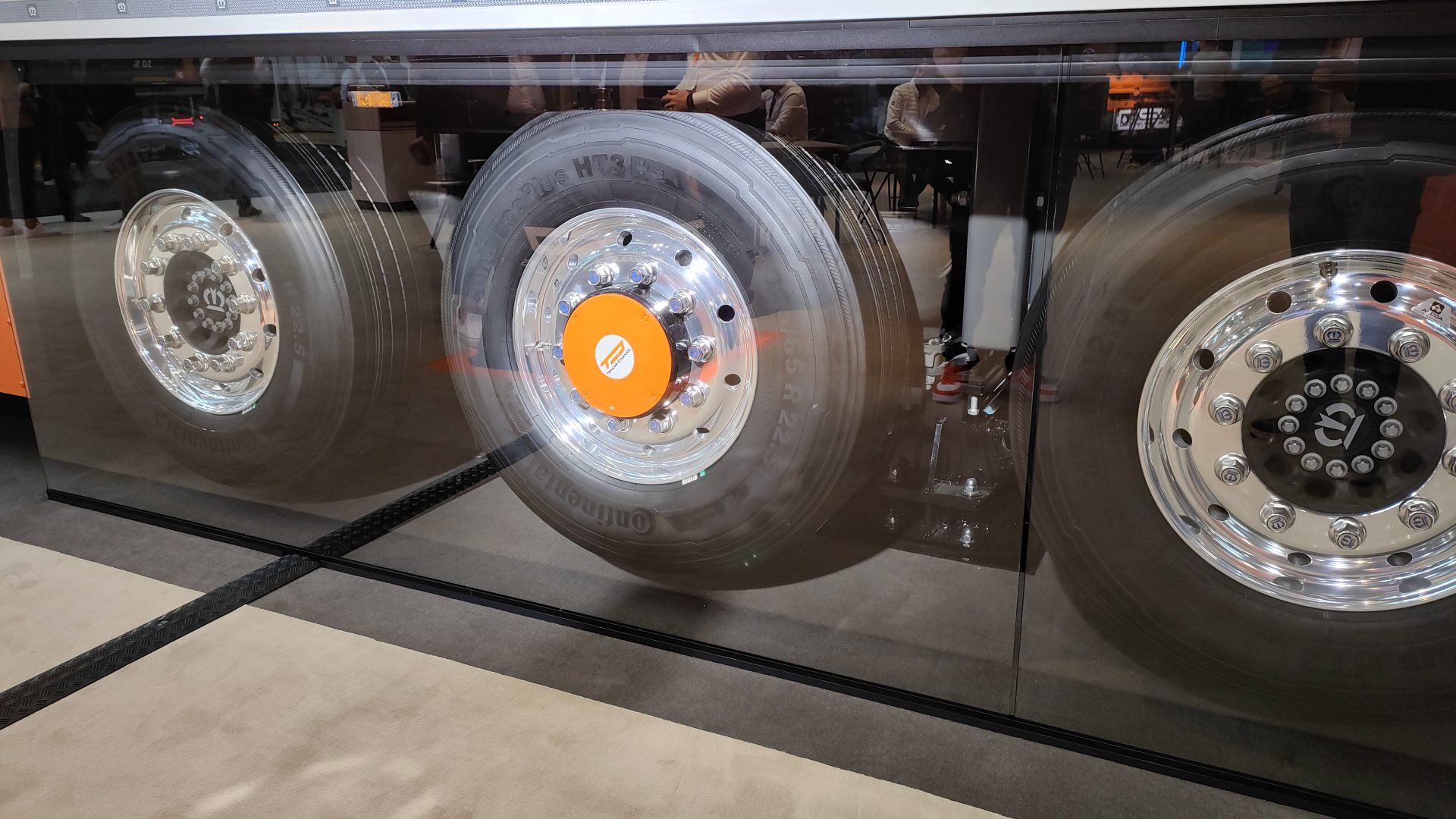
Where does the energy come from?
Our battery packs, provided by CATL, allow us to provide offer a modular solution with three levels of capacity: from 187 kWh, to 387 kWh, up to 551 kWh depending on the use case of the customer. The heart of our solution, however, is the sensorized king pin, the linking pin between the truck and the trailer. We’ve sensorized the king pin so we can feel the forces at the king pin, detect them, transform them into digital signals, and send them over to the control unit, which manages to control the axle in real time.
Does the system work with specific truck models?
The whole system is completely truck independent. It’s a plug-in system, with no cables on the truck, nothing at all. The truck and the trailer can be coupled and de-coupled several times a day. I mean that the truck can be a diesel one, electric, hydrogen one. It can even be a Scania, MAN, Volvo, and so on. There’s no difference.
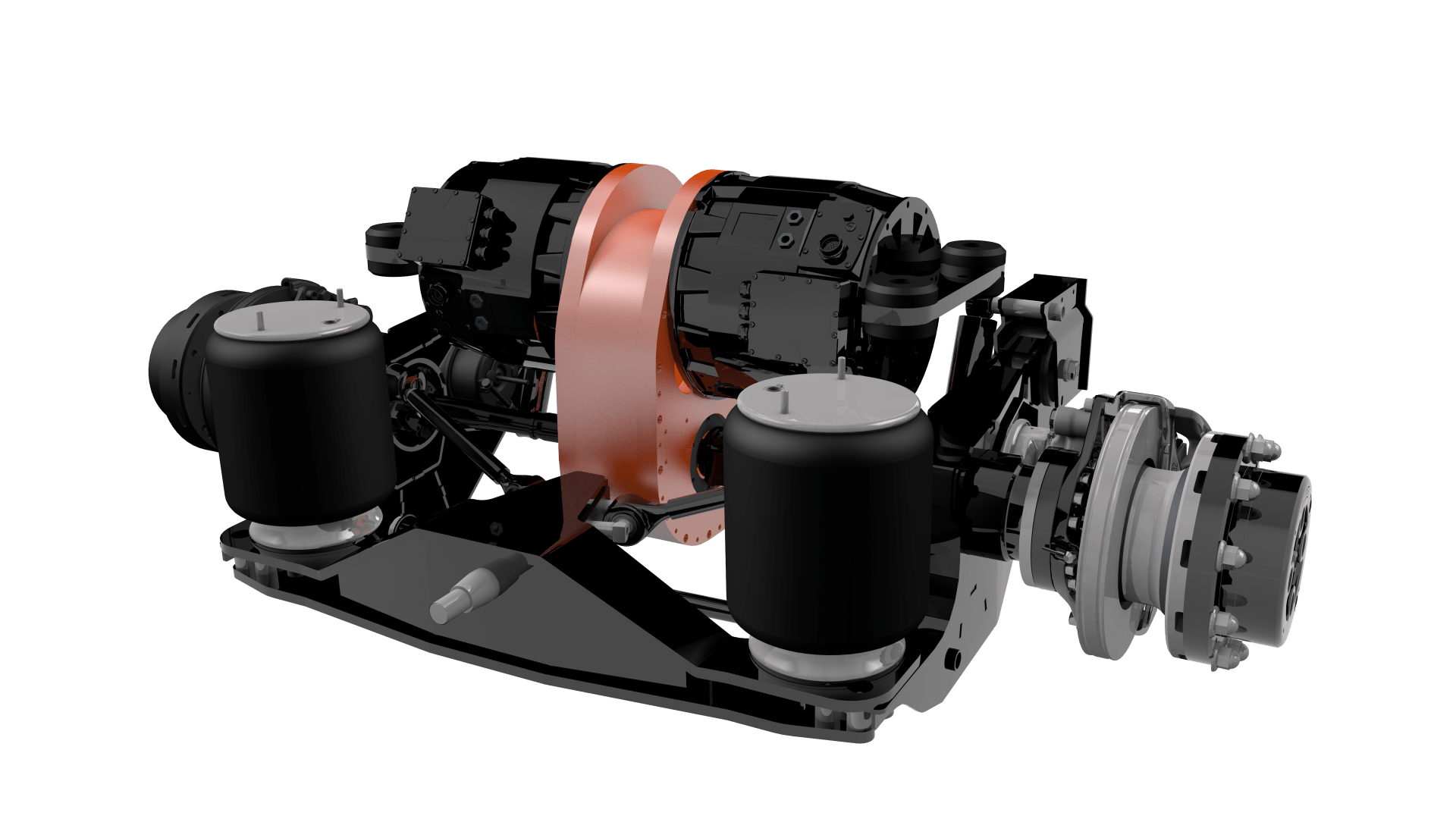
The tools to pattern the routes and calculate the TCO
Let’s come to the hard matter of price. When does the Trailer Dynamics solution become convenient for transportation companies?
These vehicles and this technology need dedicated routes. This is fundamental to create the necessary TCO from an economic perspective. For this reason, we support our customers with a performance simulation tool. By means of this tool, we can mirror reality, in terms of routes, truck type, trailer type, topography, and so on. The entire system is then capable of telling how much energy you need; how much consumption and CO2 is possible to reduce. On top of that, based on these individual data, we provide a CO2 footprint document, which is certified by TÜV, so that our customers know exactly what the energy consumption and CO2 reduction is, documented.
Battery swapping
At IAA, we also saw something interesting about battery swapping technology…
Battery swapping is an existing option that can provide real and concrete advantages when it comes to charging. In battery swapping the swap time is only 5 minutes. For logistics companies, it means that fleets can be used much more than before. It also means companies may need less vehicles compared to a conventional scenario. There are huge benefits also in terms of costs, as the batteries may be owned by the stations in this way. In other words, they become utilities. We truly think this is one of the viable alternatives in regard to charging infrastructure.
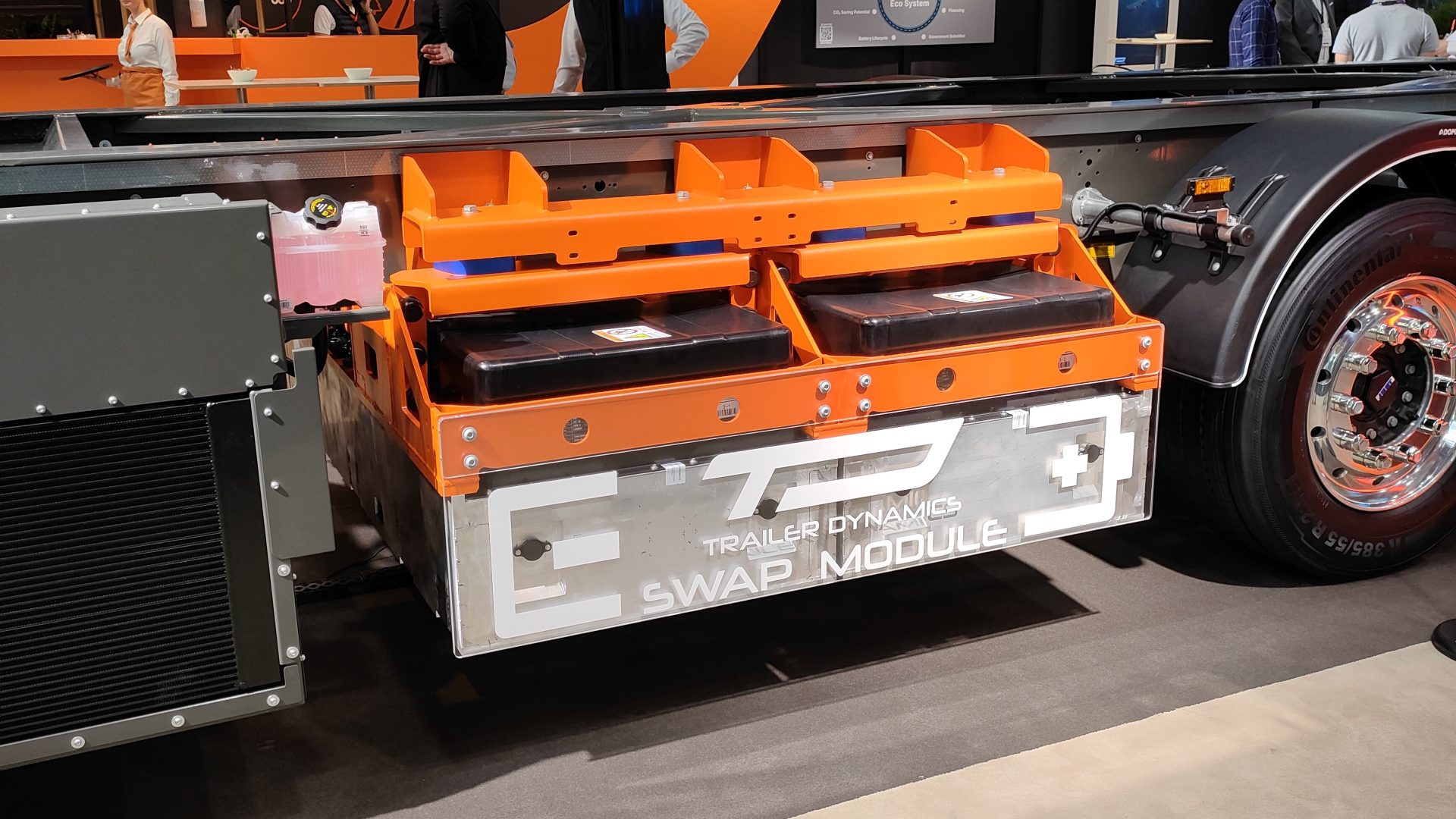
Is Trailer Dynamics you currently involved in any battery swapping project?
The project does exist already in China. It started a few months ago, we think its realization requires two to three years. Battery swapping can be applied to public or private environments. The latter means big fleet owners or big logistics companies with 200, 300 or 400 electrified vehicles. The connection to the trailers are, of course, standardized. We’re the only ones to provide this service, so currently it’s only applicable to Trailer Dynamics vehicles. Of course, if the technology works in the market, we’ll have to develop a system that can be used with different types of vehicles. This kind of solution is clearly asking for a standard.
Except for the batteries, all the other key parts of the e-kit are developed and manufactured by Trailer Dynamics?
Trailer Dynamics has developed the whole solution. As I said, the batteries are developed and supplied by CATL. The axles were developed internally, even though we’re not the manufacturers. We turn to a third company, which makes them according to our own design.
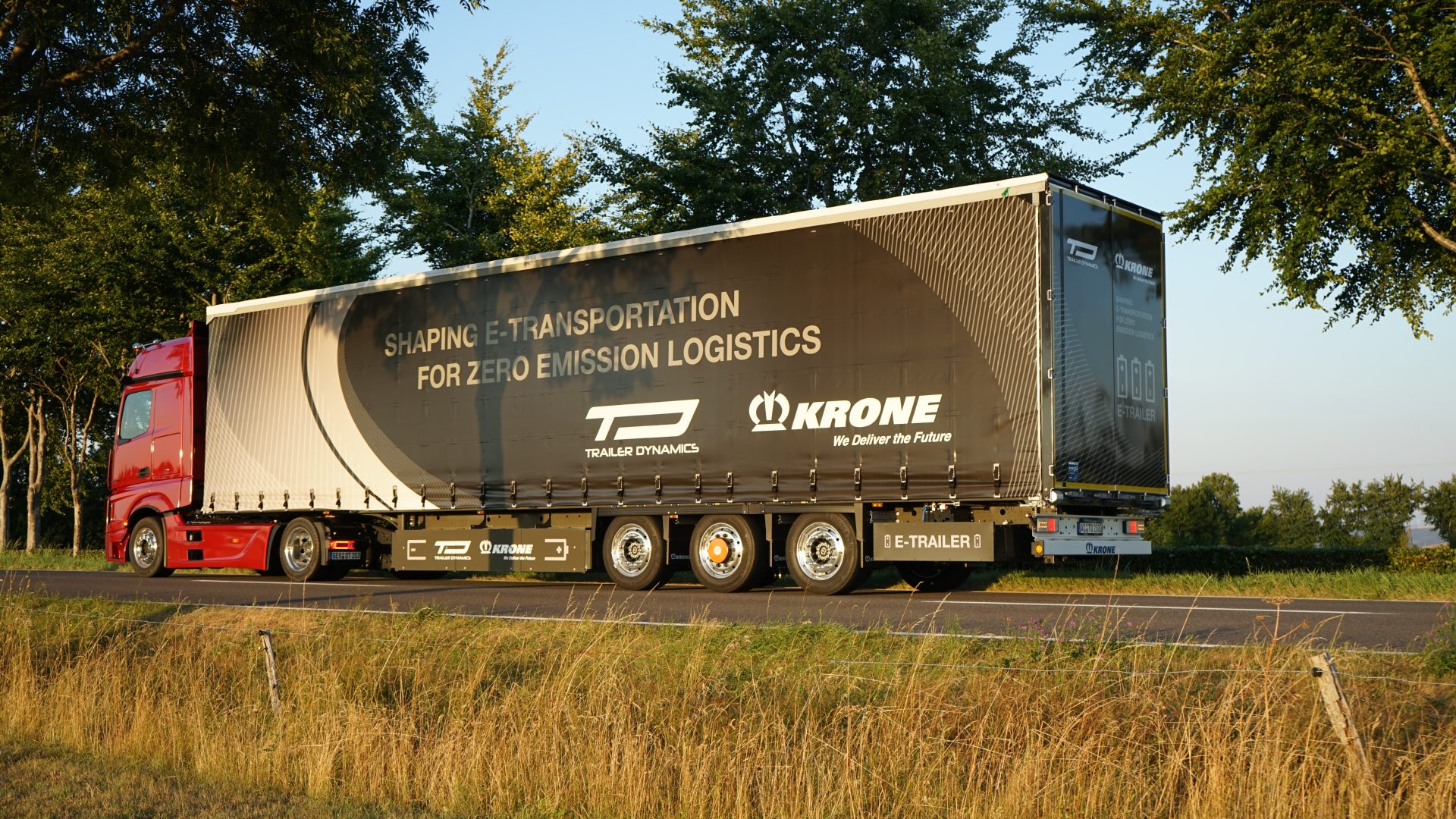
The partnership with Trane Technologies and Thermo King
Earlier this year, a strategic collaboration with Trane Technologies’ brand Thermo King was announced, with the first becoming a minority investor in Trailer Dynamics, alongside German trailer maker Krone. What’s the meaning of the alliance with a brand such as Thermo King?
We are both on a decarbonization path. We love to partner with companies which follow the same path. Both companies are working on the same idea, the same vision. This helps us to market our products. By using the system we have developed, the energy for the refrigeration unit would come entirely from our batteries.