Recycling, Scania to employ reused components on truck assembly lines
At first, Scania is using remanufactured gearboxes, which were subject to exactly the same rigorous steps and inline quality and function tests as gearboxes that are made from entirely new parts. The gearbox duly met all those requirements and could therefore be confirmed as being ‘as good as new’.
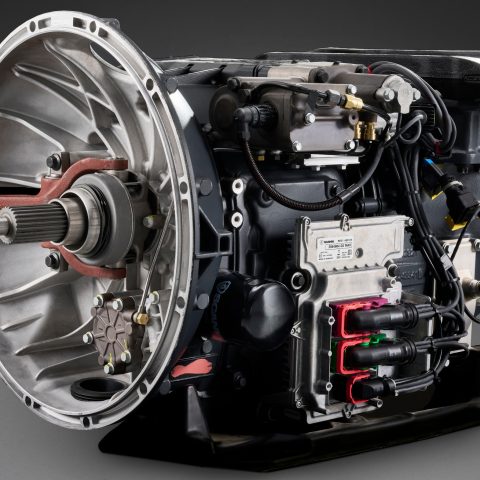
Scania has integrated reused components on its main assembly line in Sweden. The achievement is part of the iReGear joint research project with KTH Royal Institute of Technology and Scandinavian Transmission Service AB, and was made possible with funding from Vinnova, the Swedish innovation agency.
At first, Scania is using remanufactured gearboxes, which were subject to exactly the same rigorous steps and inline quality and function tests as gearboxes that are made from entirely new parts. The gearbox duly met all those requirements and could therefore be confirmed as being ‘as good as new’.
Scania’s remanufactured gearboxes
In addition, according to Scania, the remanufactured particular gearbox consumed approximately 50 percent less material and caused 45 percent fewer carbon emissions compared with gearboxes made only with new components. “What an achievement by the project and everyone involved. This remanufactured gearbox is a compelling example of how the manufacturing of heavy vehicles can become more sustainable, circular and efficient, while still retaining the highest quality standards,” commented Fredrik Nilzén, Head of Sustainability at Scania.
“This research provides the first evidence to support the argument that it is feasible to envision future manufacturing organizations seamlessly integrating manufacturing and remanufacturing operations to develop Circular Manufacturing Systems that consume fewer resources, produce fewer emissions, and cost less without compromising quality and performance”, added Farazee Asif, Assistant Professor at KTH.