Inside the new 1,000 square-metre Scania battery lab in Södertälje
With this lab, Scania can test the performance of battery packs on operational electric trucks and buses without removing batteries. Vehicles are parked close to the lab and connected to testing equipment. The test equipment is delivered by Keysight, a leading test and measurement equipment provider for e-mobility among other things.
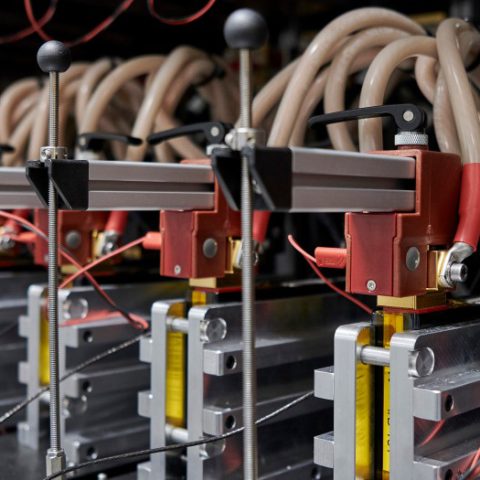
The newly refurbished Scania battery lab in Södertälje is up and running. It is quite an important facility within the company’s headquarters in Sweden, alongside the new battery assembly plant (equipped with ABB robots), as well as the test track optimised for electric and autonomous vehicles that will be ready in the coming years.
“It was truly demanding to try and specify the needs we have today when the construction began a few years back. Some things weren’t even in people’s minds back then. But we see a need to intensify battery testing and tailored deployment. That is why we invest EUR 15,5 million in this new battery laboratory”, said Håkan Örnhed, Head of Test Cell Operation Battery/E-components.
Scania battery lab: three 250-square metre test halls
The facility consists of three 250-square metre test halls for battery cells, modules and packs, and each area is its own fire compartment for safety. The increase in capacity compared to the “old” laboratory is huge. And it is called for, as before, a battery could perform 1kWh, and soon Scania will be able to offer vehicles with batteries capable of 1,000 kWh. About 20 test rigs are currently in the lab.
With this lab, Scania can test the performance of battery packs on operational electric trucks and buses without removing batteries. Vehicles are parked close to the lab and connected to testing equipment. The test equipment is delivered by Keysight, a leading test and measurement equipment provider for e-mobility among other things. Keysight has delivered a holistic solution with products for testing batteries at cell level, but also at module and pack level, including the software to control the test stands as well as program and monitor battery tests.
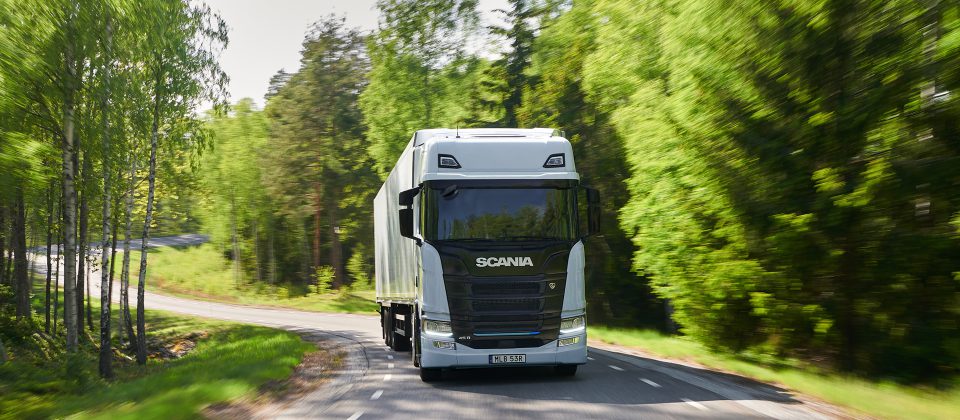
Testing batteries? It takes time…
The lab can carry out tests on 170 objects simultaneously. The thing with testing batteries is that it takes time. “A lifespan test takes two years. It is the equivalent to seven years on the road. We also have this enormous chamber where we can put a whole power train, if we want to. If we use that instead of real-life winter tests, we save a lot of money”, Scania states. The lab primarily focuses on battery performance and lifespan evaluation in varying climate conditions from -40°C to 70°C. Scania’s engineers examine and identify the best operational conditions for the battery, considering things such as temperature setpoint, state of charge window and charging power profile for tailored utilization in optimizing battery life and customer needs.

“We have trained for this massive transformation and industrial upscale for some years, now it is time to show it”, concluded Jakob Öman, Head of Battery Cell & Module Testing at Scania. And more is to come. A place to prepare, where we add sensors and similar equipment, is on its way. “We also try tear-down, where we dismantle the cell into pieces. I wouldn’t be surprised if we need even more space in a few years. It’s mostly about how fast we can build new facilities”.