Mercedes, the eActros begins series production in Wörth
Before the eActros comes to the Future Truck Center - the production hall in building 75, which was officially put into operation with the start of today's series production - for its electrification, it will be flexibly manufactured on the existing assembly line alongside trucks with conventional drive systems.
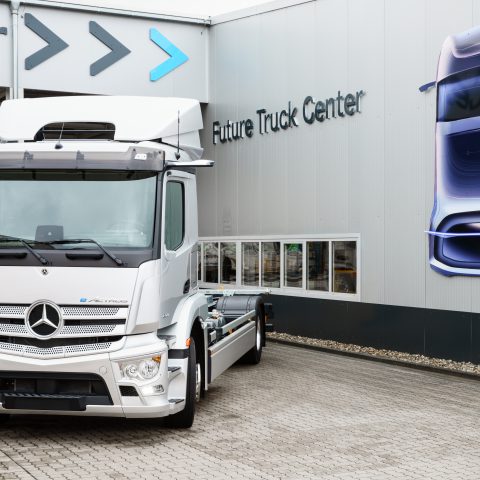
Yesterday, October 7, Mercedes inaugurated series production of the eActros. The very first battery electric truck manufactured by Mercedes-Benz will be produced in Wörth-am-Rhein, as confirmed a couple of weeks ago by Daimler Truck’s top management during the ‘Shaping the Now and Next’ live event. Next year – in the second half f 2022, to be precise – the eEconic BEV waste management truck is expected to follow. The two trucks should share most of the components, including the battery packs, which will be manufactured in Mannheim.
«Today’s start of the eActros series production is a very solid proof that we’re serious about zero-emission transport», commented Karin Rådström, Member of the Board of Management of Daimler Truck, responsible for Mercedes-Benz Trucks (to the right, in the picture below). «The eActros, Mercedes-Benz’ first battery-electric serial truck, and our related services are a major step for us and for our customers towards CO2-neutral road haulage. And the vehicle also has a very special significance for the Wörth plant and its long-term orientation: the future of Mercedes-Benz truck production is starting today. We want to greatly expand the series production of our electric trucks here».
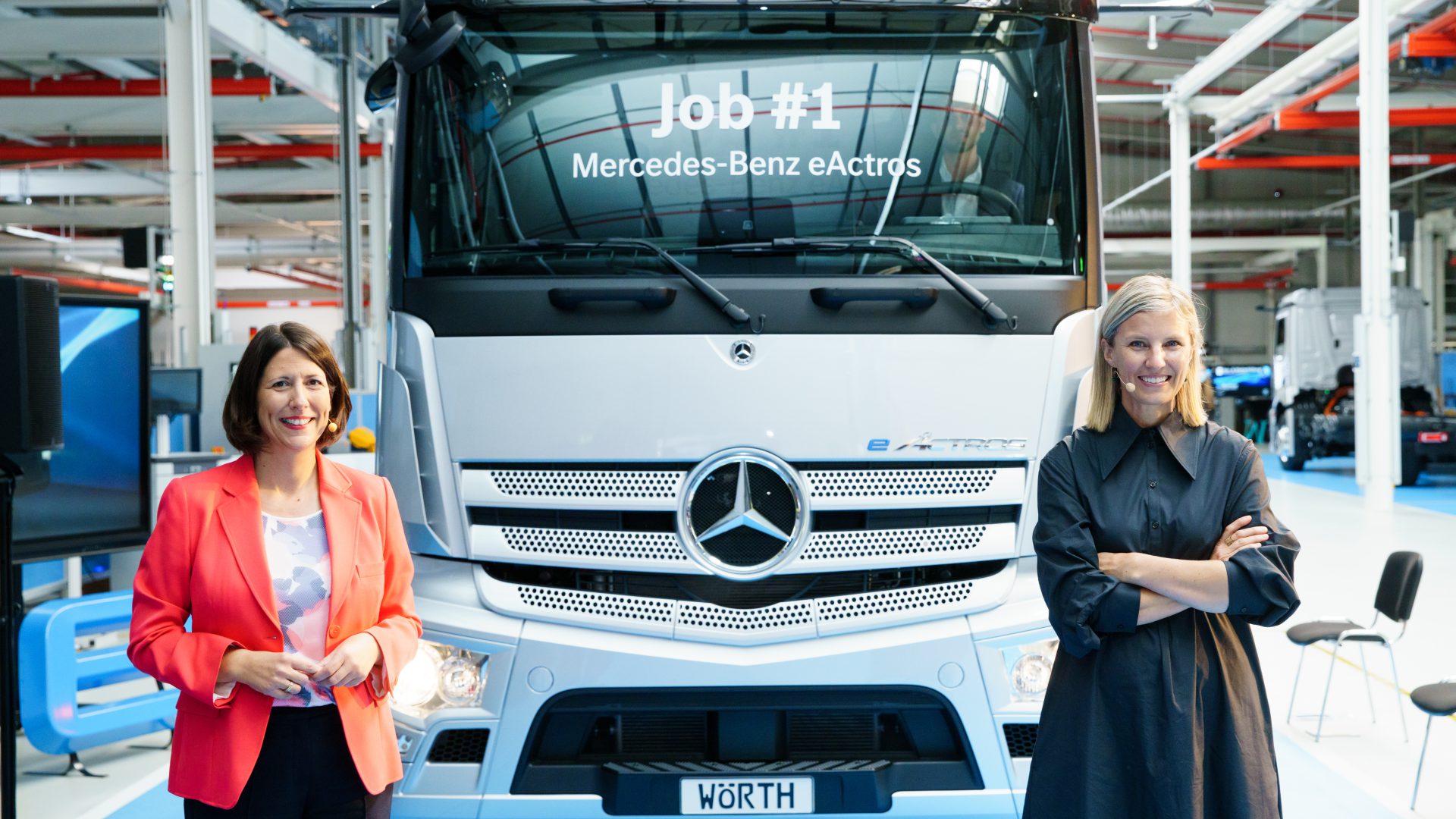
The eActros in series production, a key role for the Future Truck Center
«The technology shift in our industry towards locally CO2-neutral trucks also means an immense change for our locations and production. The start of eActros series production is not an everyday ramp-up for us, but a real new beginning», added says Sven Gräble, Head of Mercedes-Benz Trucks Operations. «Our so-called fullflex concept makes it possible to integrate the e-trucks into the existing production. In this way, the plant is able to efficiently and even more quickly adapt to the respective market demand and reliably meet the demanding quality standards of Mercedes-Benz».
Before the eActros comes to the Future Truck Center – the production hall in building 75, which was officially put into operation with the start of today’s series production – for its electrification, it will be flexibly manufactured on the existing assembly line alongside trucks with conventional drive systems. Basically, the assembly of different vehicle types will take place in an integrated manner as far as possible and the basic structure of the vehicle will be built on one assembly line – regardless of whether a conventional combustion engine or an electric powertrain is installed.
Talking about powertrain, a few days ago Daimler communicated that the first components had been produced in Wörth, waiting for the official vehicle production start. More into details, the Mercedes-Benz plant in Mannheim has begun to assemble the battery packs, while the plant located in Kassel has started assembling the electric axles. Another plant, this time in Gaggenau, is manufacturing the associated transmission components.
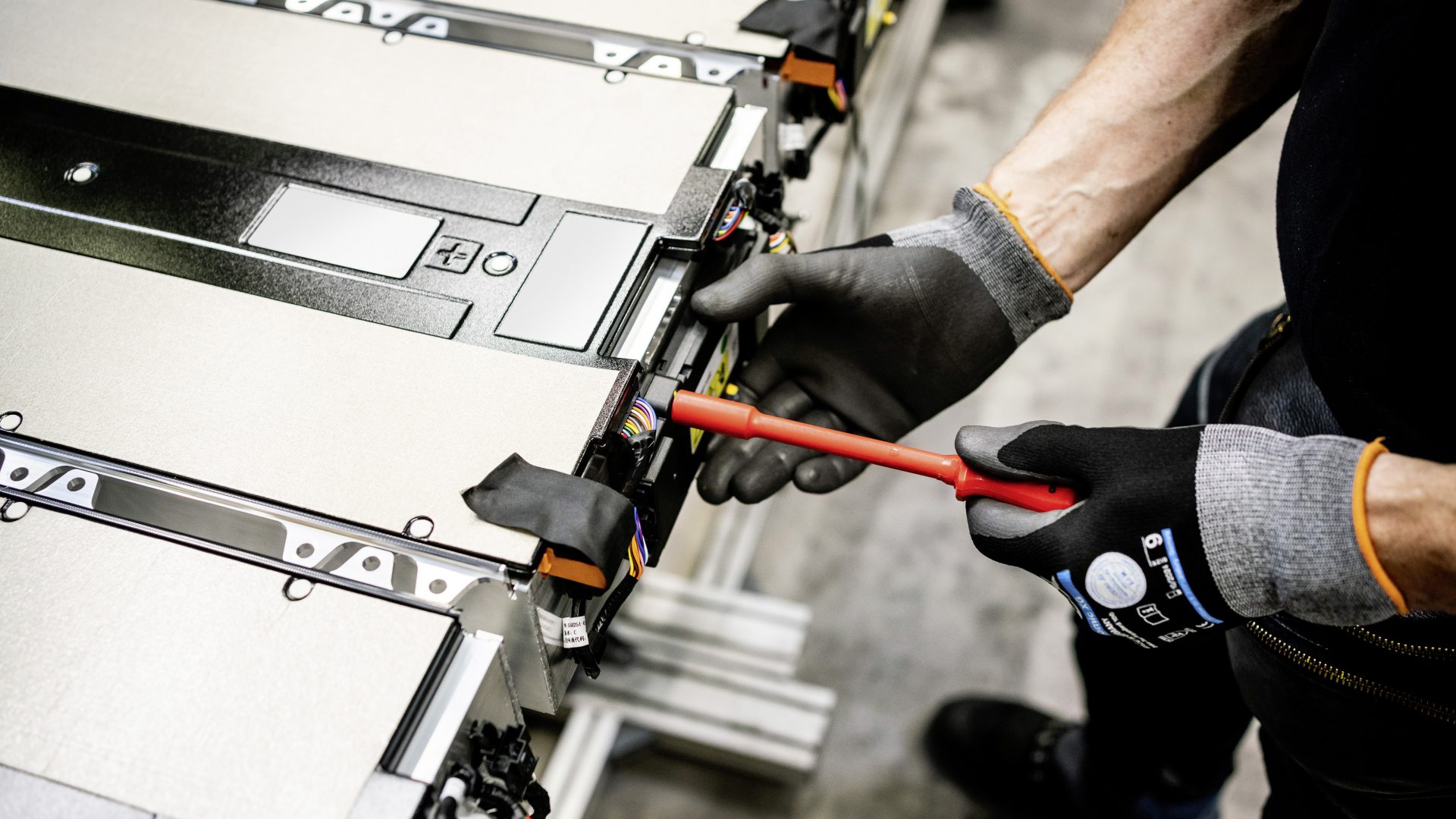
A closer look at the electrical powertrain
A battery pack for a series-produced eActros consists of six individual battery modules. A completely assembled pack is almost 2.20 metres long, 75 cm wide and 55 cm high. The complete electric axle, consisting of the axle bridge, the electric motor and the shiftable transmission elements, is assembled in Kassel. The drive unit, including the two-speed transmission, is pre-assembled in parallel. After the core axle is pre-assembled, the entire drive unit, including the two-stage transmission, is attached to the axle. Before the electric axle is prepared for shipment, it is subjected to a function and high-voltage test. These tests especially examine electrical safety and noise properties. As for the transmission-related mechanical components and the associated housings, the main challenge is that the transmission parts and the steel and aluminium housing components have to be made as precisely as possible because they are specified to extremely tight tolerances. This is necessary in order to ensure the electric axle works perfectly and has optimal noise properties.