Ahead of serial production, Mercedes is producing key components of the brand-new eActros 600
The Mercedes-Benz plant in Gaggenau, which specializes in transmissions for heavy-duty commercial vehicles, is currently developing into a center of expertise for electric drive components. In addition, the Mercedes-Benz plant in Kassel is assembling the new generation of the e-axle for the eActros 600.
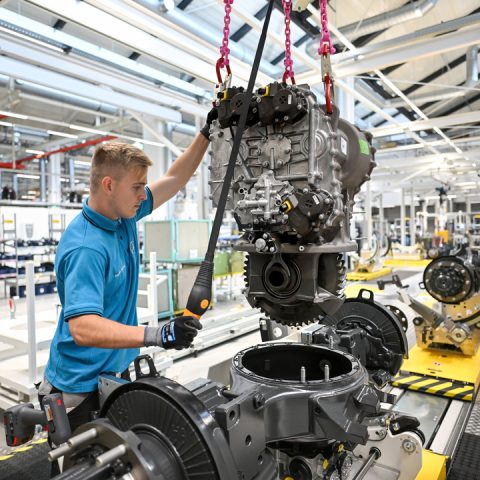
We’re getting closer to the official start of series production of the new Mercedes-Benz Trucks flagship, the eActros 600, at the company’s plant in Wörth. Ahead of this, the Mercedes-Benz plant in Gaggenau, which specializes in transmissions for heavy-duty commercial vehicles, is currently developing into a center of expertise for electric drive components.
Since 2021, key parts for the e-axle (a unit that combines the axle, motor and transmission and represents the electric powertrain) of the eActros 300/400 for distribution transport and the eEconic have been manufactured in Gaggenau. The same will apply to the central components of the new generation of the electric axle that will power the eActros 600. In addition, the bodyshell components for the cab of the eActros 600 are also manufactured in Gaggenau, while the Mercedes-Benz plant in Kassel, the global center of excellence for conventional axles and electric drive systems, is assembling the new generation of the e-axle for the eActros 600.
Mercedes eActros 600: some more production details
The scope of supply includes, among other things, structural body parts such as the rear panel, roof frame, bulkhead and cross members, as well as various reinforcements. These are carry-over parts that are already used in conventionally powered trucks. The bodyshell expertise of the plant thus “carries” the outer skin of the newly designed cab of the new battery-electric long-haul truck.
A completely new production plant with automated processing centers has been set up in Gaggenau. During the procurement phase, the virtual commissioning of these centers enabled the processing to be simulated on so-called “digital twins”. This process results in enormous time savings compared to a conventional production plant setup process.
“No future without the past! At the Mercedes-Benz plant in Gaggenau, tradition and transformation go hand in hand. We are proud to apply our decades of experience in the manufacture of high-precision transmission components to the new electric powertrain. Together with our colleagues at the assembly plant in Kassel, our plant is making an important contribution to emission-free mobility”, stated Thomas Twork, Plant Manager Mercedes-Benz Plant Gaggenau.