MAN is working on making the most out of e-truck batteries (including recycling the raw materials)
Actually, the company expects that electric trucks will have a share of 60% in distribution applications and 40% in long-haul transport in 2030. So, it's quite important to treat batteries in the most efficient way from square one.
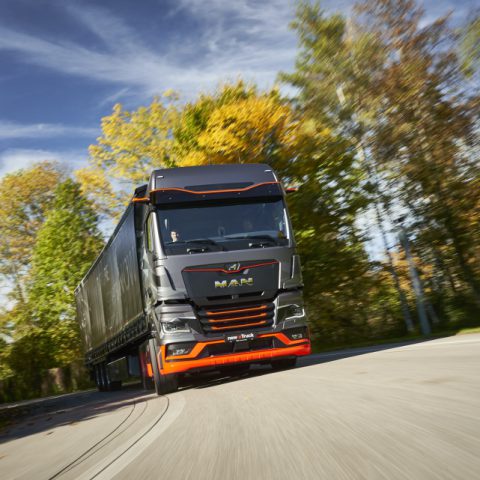
Within MAN Truck & Bus electrification strategy, batteries play quite an important role. It is no coincidence that the German manufacturer is shaping its own battery production factory, whose inauguration is foreseen by 2025. In addition MAN wants to make the most out of e-truck (and e-bus) batteries by extending their life in the first step and, if this is no longer possible, by recycling the raw
materials contained in them.
We know that MAN strongly believes in BEV trucks for the future of goods transportation. Actually, the company expects that electric trucks will have a share of 60% in distribution applications and 40% in long-haul transport in 2030. So, it’s quite important to treat batteries in the most efficient way from square one. More into details, the analysis starts with the first life of the battery in the vehicle. The focus here is on training customers to drive, charge and use the vehicles so that the load on the battery is minimised.
How’s MAN treating traction batteries
The batteries that come back to MAN after use in the vehicle are analysed intensively. In the event that the battery packs can no longer be used as so-called traction batteries, they are forwarded to secondary applications. Currently, there are three options for this: a second use in the vehicle after factory repair, a second battery life, for example as buffer storage of solar or wind power installations, and finally, the recovery of battery raw materials for new batteries in the sense of recycling.
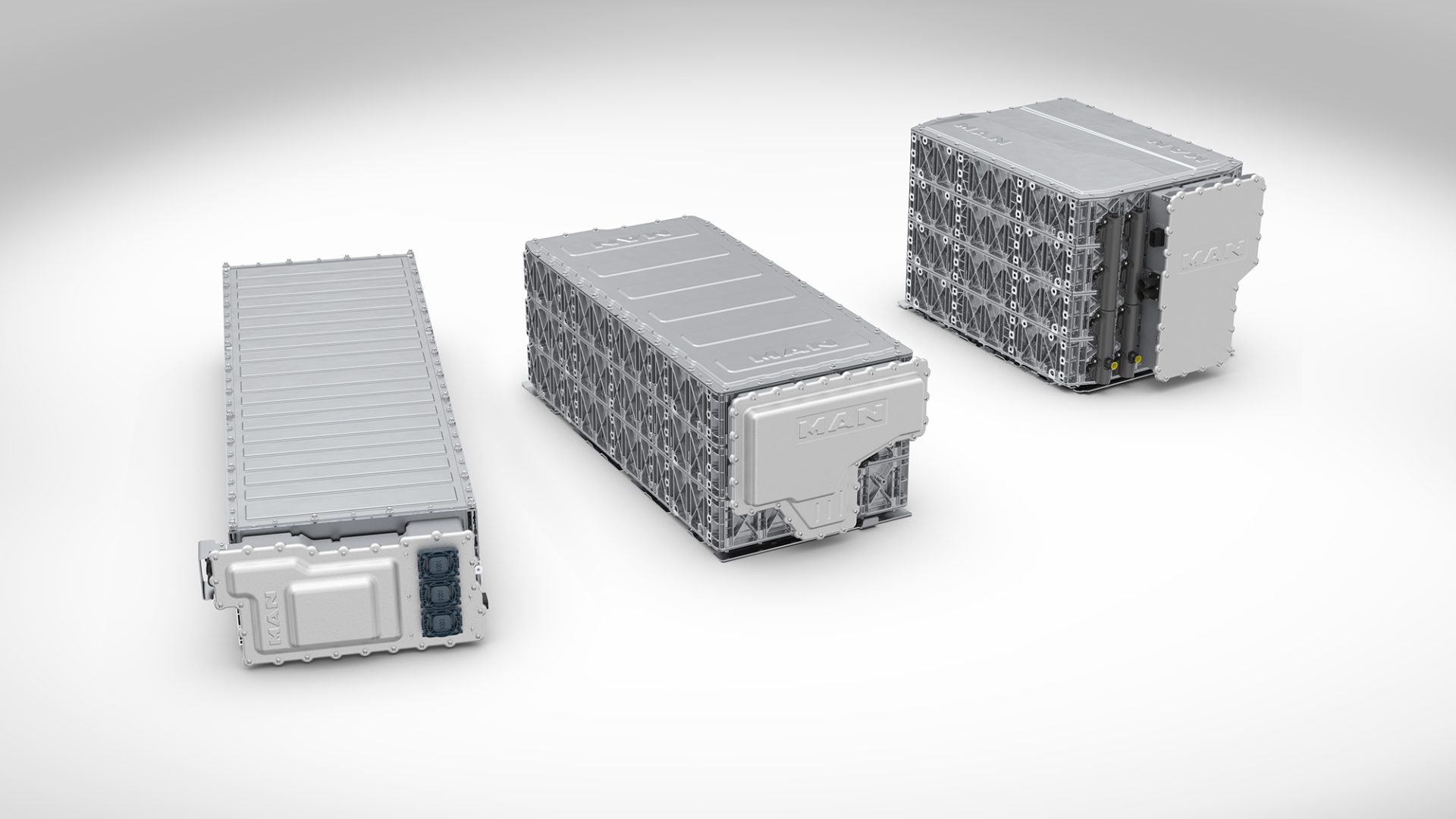
MAN is currently working with various partners and the University of Kassel on real projects to evaluate whether used truck batteries are suitable for stationary storage systems. For this purpose, around 120 truck battery packs with an energy content of 18.6 kWh per pack are being handed over to a storage system manufacturer. In the current project, the focus is on energy storage systems for industrial
companies.
When recycling comes into play
Recycling comes into play after the 2nd life of the batteries or in the event that batteries are no longer suitable for storage applications after vehicle use or an accident. MAN’s stated aim is to achieve a closed cycle for battery raw materials – from cradle to cradle. The goal is to use the raw materials recovered by the recycling partners, such as nickel, manganese, cobalt or lithium, in the new production of batteries. At present, the recycling rate is more than 70% in relation to the weight of the battery. For recycling, MAN prefers a mechanical process followed by hydrometallurgical treatment.