The weight of powertrain on total cost of electric commercial vehicles. What can we learn from the Chinese scenario?
When dealing with electric commercial vehicles, the cost of powertrain components accounts for up to 80 percent of total vehicle cost. This is maybe the main outcome of Maya Xiao’s research on the Chinese automotive sector. We made her some questions.
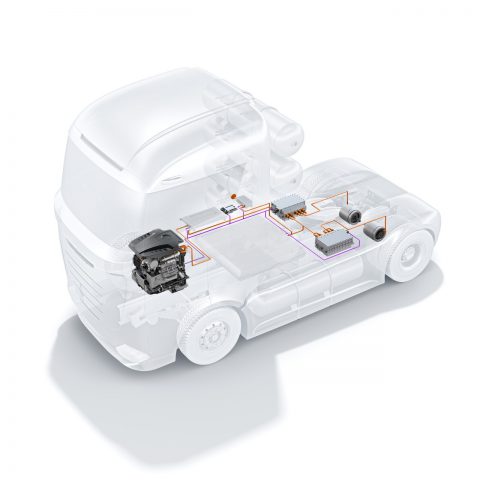
When dealing with electric commercial vehicles, the cost of powertrain components accounts for up to 80 percent of total vehicle cost. This is maybe the main outcome of Maya Xiao’s research on the Chinese automotive sector. Such a study allowed Maya Xiao to draw some interesting conclusions and outline forecasts and trends that might be also applied to Western markets as well.
Starting from her own article – Maya Xiao is the China-based lead analyst for Interact Analysis’ Li-ion battery and forklift research – we made her some questions you can find later on in this post.
Powertrain accounts for up to 80% of electric commercial vehicle cost
First of all, let’s recap the main highlights of the above-mentioned study. «The purchase price of an electric commercial vehicle in China is currently about double that of a conventional ICE vehicle», Xiao wrote. It’s the high cost of powertrain components which has driven up electric commercial vehicle pricing. Taking the example of light duty vehicles in China, in the 4.5 ton range the powertrain accounts for 70-80% of the total vehicle cost. For a similar conventional vehicle, it’s 50-60%. The scenario is not that different when talking about heavy-duty vehicles.
Within powertrain elements, it’s not difficult to say that batteries are the key component. According to Xiao’s study, lithium iron phosphate (LFP) batteries, used to power commercial vehicles in China, have increased energy density and decreased price in the last few years. Such trend is supposed to continue in the next years, with direct consequences on total vehicle cost.
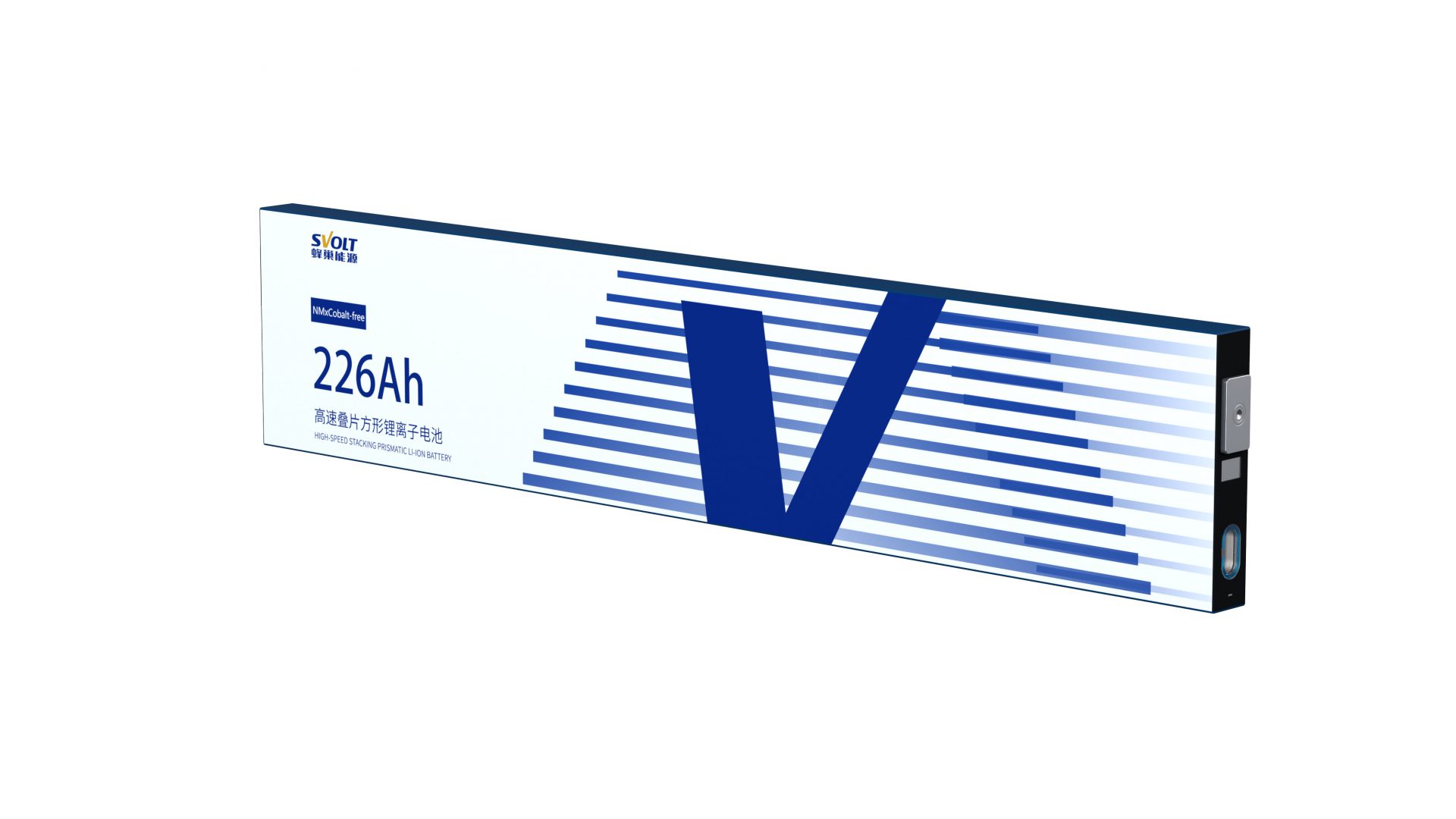
Newcomers entering the automotive market
Similarly, the cost of other key powertrain components, such as drives and motors, is expected to go down also due to a higher number of producers and suppliers entering the market. Xiao reports the examples of Bosch, Innovance or INVT, the latter coming from industrial automation. Technological improvements will also allow designers to reduce complexity and use less components without affecting performance at all. «We expect to see the introduction of transmission technology into this sector, which will mean larger vehicles will be able to be equipped with smaller, lighter, and less expensive motors», Xiao wrote in her article. Finally, we are experiencing several agreements between OEMs and battery manufacturers, with the latter gaining experience and orders in the coming years.
Starting from the Chinese situation, let’s see what might happen elsewhere.
Lead analyst Maya Xiao provided answers to our questions
How’s the EV market in the light- and heavy-duty commercial vehicle segment doing in China? Is it booming despite the cost issues you mentioned in your article?
«We hold a positive opinion of electrification in light- and heavy-duty trucks in China in the long run, despite the fact that EV truck sales have fluctuated in recent years due to the withdrawal of government subsidies. With the national objectives of Carbon Emission Peak by 2030 and Carbon Neutrality by 2060, transportation is among major industry sectors pushed by government to limit its carbon emissions. Despite degrading fiscal incentives for vehicle purchases, a series of government incentives remain in place to drive the industry’s sustainable growth. These include favourable policies for charging infrastructure penetration, local government subsidies per EV according to annual operation mileage, subsidy for fuel-cell vehicles and so on. On the other hand, manufacturers throughout the value chain – including key component suppliers, vehicle manufacturers, and distributors – strive for cost reductions via renovations in technology and business models to drive down total ownership costs. Ultimately, it is an inevitable trend that commercial vehicles in China will move towards electrification».
Is the issue of raw materials needed to produce batteries a key one when thinking of a broader EV market in the near future? How’s China facing such issue?
«Battery raw materials are the upstream industry in the new energy vehicle industry chain. In theory, their price will be transmitted to EV manufacturers through battery manufacturers, which will affect the price of consumers buying electric vehicles. If price rises continue, at the macro level, it may even affect the time for the cost levelling of national electric vehicles and fuel vehicles. But so far, no car companies have raised vehicle prices because of the battery costs. At present, the industry believes that the rise in the price of raw materials will not be transmitted to the price of new energy vehicles in the short term, because end consumers are still relatively sensitive to the price. Battery manufacturers have also made a long-term outlay for the supply of raw materials (including taking shares in or acquiring mines) and have avoided possible risks through technology research and development (such as optimizing the chemical composition of batteries). In the long run, it is a general trend that battery costs continue to decline, and electric vehicle prices continue to decline alongside them».
In the long-term, if there is a shortfall in the numbers of motors that traditional auto suppliers can make, this is definitely an opportunity for industrial automation vendors
Maya Xiao, Interact Analysis lead analyst
An opportunity for industrial automation vendors
“Major suppliers of motors and drives for industrial automation have moved in on the EV component supply market”, you wrote. Is this a key factor to fulfil the higher production and request for electric commercial vehicles?
«At present, we do not have specific figures on the market share of these industrial automation vendors but, according to market feedback, the products of these enterprises are indeed being installed on electric vehicles more and more. Industrial automation vendors are seeing great potential in the electric commercial vehicle market, and so are entering this market, and competing with traditional auto suppliers. The situation now is not that there is a shortage in component supply, but that industrial automation vendors are trying to make an impact in an emerging market. In the long-term, if there is a shortfall in the numbers of motors that traditional auto suppliers can make, this is definitely an opportunity for industrial automation vendors».
Thinking of other areas (Europe, the US) which lessons could be learned based on the current situation in China?
«The Chinese market has shown how effective subsidies and a positive policy landscape can be at driving a behavioural shift in fleets to go electric, particularly for urban delivery and last mile. There is no doubt that, as battery prices decline, the European market can follow the same course as OEMs scale production and governments begin to heavily push for decarbonisation».