We’ve seen the new Cummins’ Powertrain Test Facility in Darlington, UK
“The new centre enables Cummins to develop and test a wider range of vehicles and machinery powered by hydrogen, renewable natural gas, advanced diesel, or battery electric”, told us Jonathon White, Vice President, Engine Business Engineering. Collaborations with OEMs and customers are crucial in Cummins' on-highway strategy. Our report from Darlington.
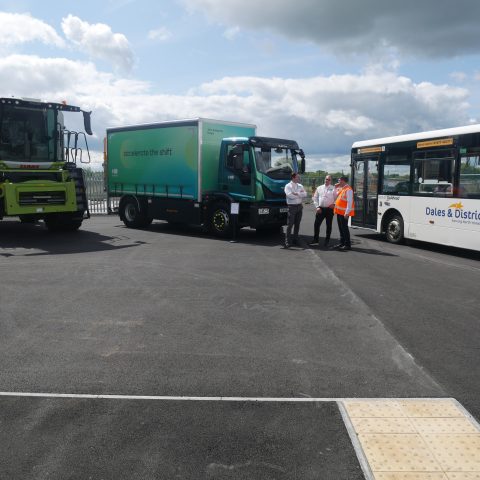
To some, it may seem like the egg of Columbus (pardon the pun), but to develop technologies without verifying safety levels and implicit risks would be fruitless, to say the least. Whether we are referring to the burning of battery packs, which must be submerged in water as a precautionary measure, or the flame spread in the event of hydrogen combustion, the behavior of the propulsion system must be tested along with the vehicle.
And it is from Columbus, Ohio, that the awareness originates, which we visualized and explored at the Powertrain Test Facility, located at Cummins’ European headquarters in Darlington, UK. Jonathon White, Vice President, Engine Business Engineering, said: “The new centre enables Cummins to develop and test a wider range of vehicles and machinery powered by hydrogen, renewable natural gas, advanced diesel, or battery electric.” How important is this new structure? We asked Felipe Rocha, Cummins General manager Europe On-Highway. “Real-world emissions are currently receiving significant emphasis. This facility enables us to achieve more precise testing and validation. Additionally, we recognize the substantial potential for collaboration with OEMs and customers here. Many OEMs are exploring the development of diesel or battery-powered electric solutions independently, but our test center offers an opportunity for joint efforts. OEMs can bring their equipment and powertrains to our facility for comprehensive testing. This integrated approach allows us to conduct testing and validations more efficiently, often consolidating what would traditionally be two separate processes into one. This efficiency not only saves time but also enhances the overall development and validation process.”
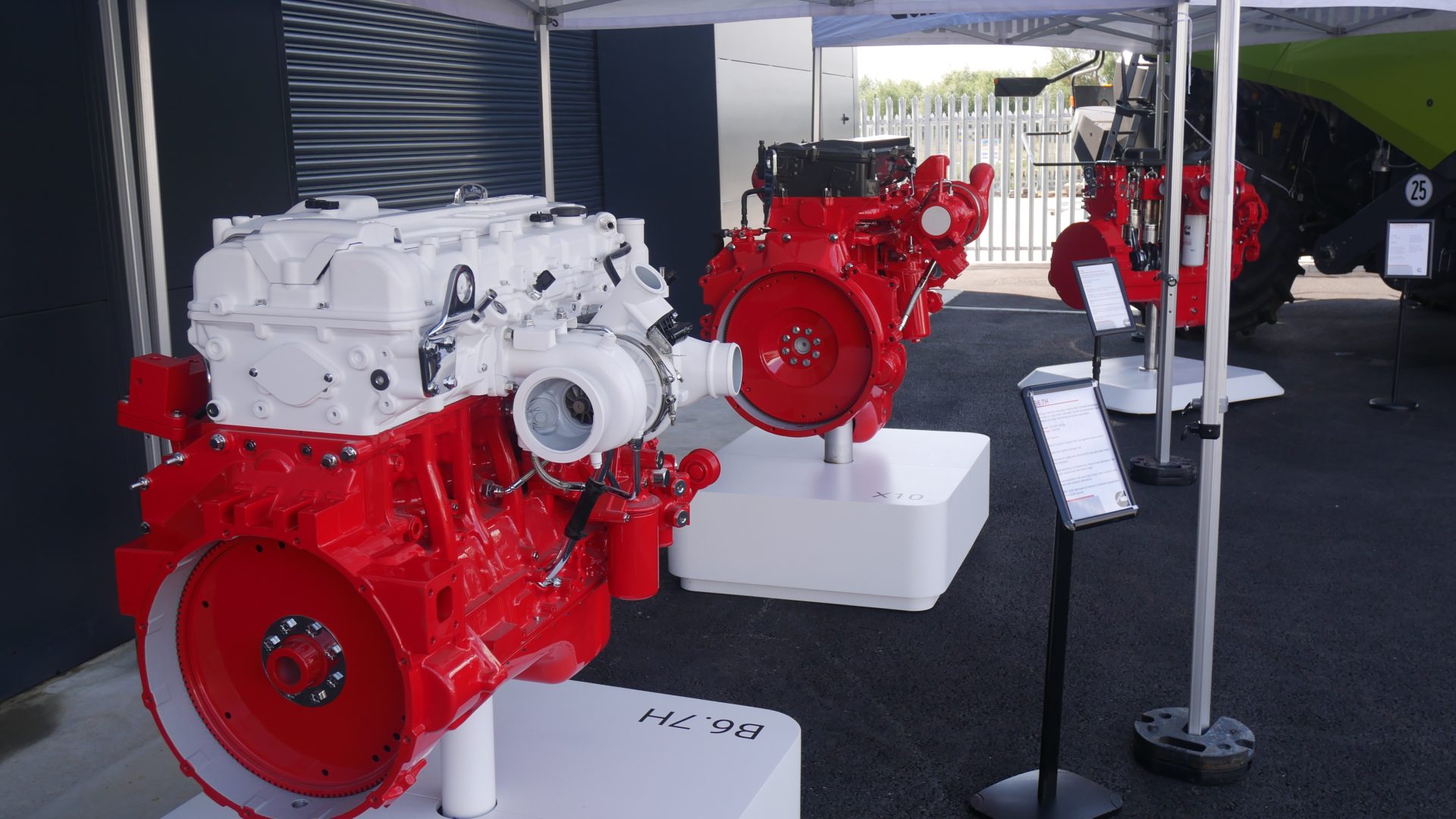
Cummins increases its footprint in Darlington, England
As we mentioned, we are in Darlington, County Durham, England, where Cummins has located its main engine and exhaust after-treatment plant and technical operations for the European market. Starting from the premises, Cummins focused on some specific goals: to enhance vehicle-level CO2 emission measurement, integrate engine-transmission-axle testing, ensure accurate fuel consumption tracking, develop fuel-agnostic testing facilities, accommodate a wider range of duty cycles, and measure a broader and lower range of emissions. Tom Partridge, Product Development Director, basically the Director of Laboratory Operations in Darlington, summarised for us the features of the vehicle test building.
“In 2018, Cummins recognized the need for a state-of-the-art facility capable of advancing development beyond Euro 6 standards and into Euro 7, as well as accommodating new technologies. Our research indicated a shift from traditional engine development to a more integrated system approach within vehicles. This insight drove the creation of our powertrain testing facility, reflecting the industry’s focus on powertrain advancements. The increasing attention to vehicle-level integration and precision in testing was the catalyst for developing the powertrain facility. Recognizing that the majority of automotive advancements were concentrated on powertrain systems, we aimed to align our capabilities accordingly. Thus, the powertrain facility was conceived to meet these evolving demands. The project officially commenced in early 2020. However, the COVID-19 pandemic caused significant delays.” And, regarding the design concept and planned applications for the Testing Centre, Partridge points out: “We built the facility to be agnostic, allowing us to test any fuel that powers vehicle machines, including natural gas and hydrogen. While we haven’t implemented it yet, we plan to introduce a battery emulator for testing EV systems.”
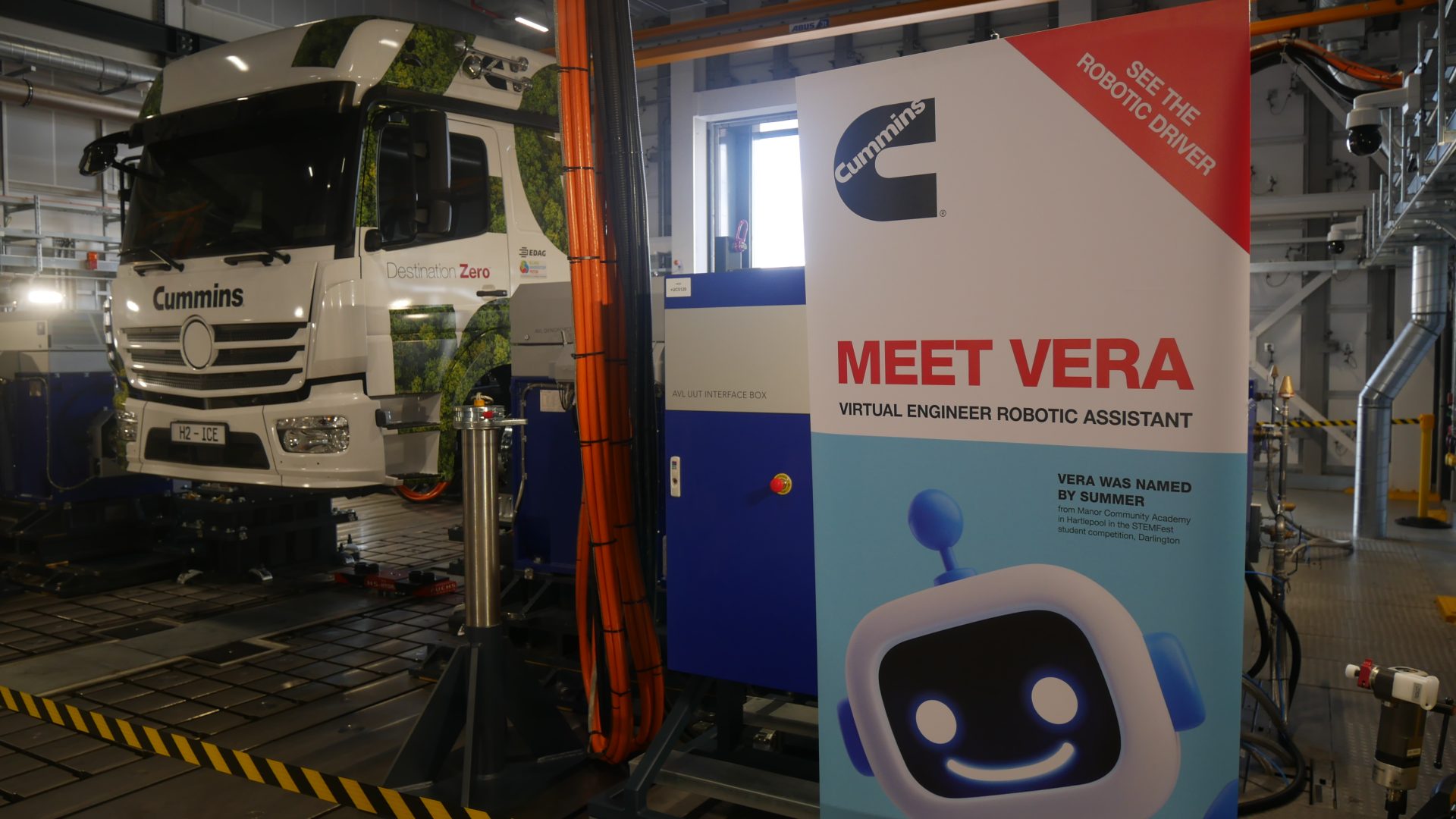
Cummins Powertrain test bed capabilities
The general capabilities of the facility include 2WD and 4WD powertrain testing, as well as heavy, medium, and light-duty testing, with fuel flexibility for diesel, hydrogen, and CNG. Energy consumption testing is conducted, focusing on VECTO optimization and driveline component tests. Transmission and driveline capabilities encompass transmission certification, drivability optimization, manual and automatic transmission compatibility, direct torque measurement of 6kNm and up to 60kNm via a 2-speed mechanism, and constant velocity input shafts up to 40kNm. Emissions testing features emission measurement capabilities with PEMS, a fixed emissions analyzer bench, and enhanced PEMS development. Vehicle simulation and testing include drive cycle simulation, inertia and road-to-lab drive cycle simulation, road grade and incline simulation, e-axle efficiency tests, and battery testing and validation.
The facility also boasts advanced control and automation systems, start-stop capability, asynchronous regenerative dynos. The capabilities of the vehicle under test include a wheelbase ranging from 300 mm to 6700 mm, a hub fan width between 1600 mm and 2480 mm, a maximum weight of 28,000 kg, a maximum continuous power output of 450 kW, and a height-adjustable front axle for agricultural tractors. Additional features include drive load units, inline testing capability, and motorizing and start-stop testing capability.
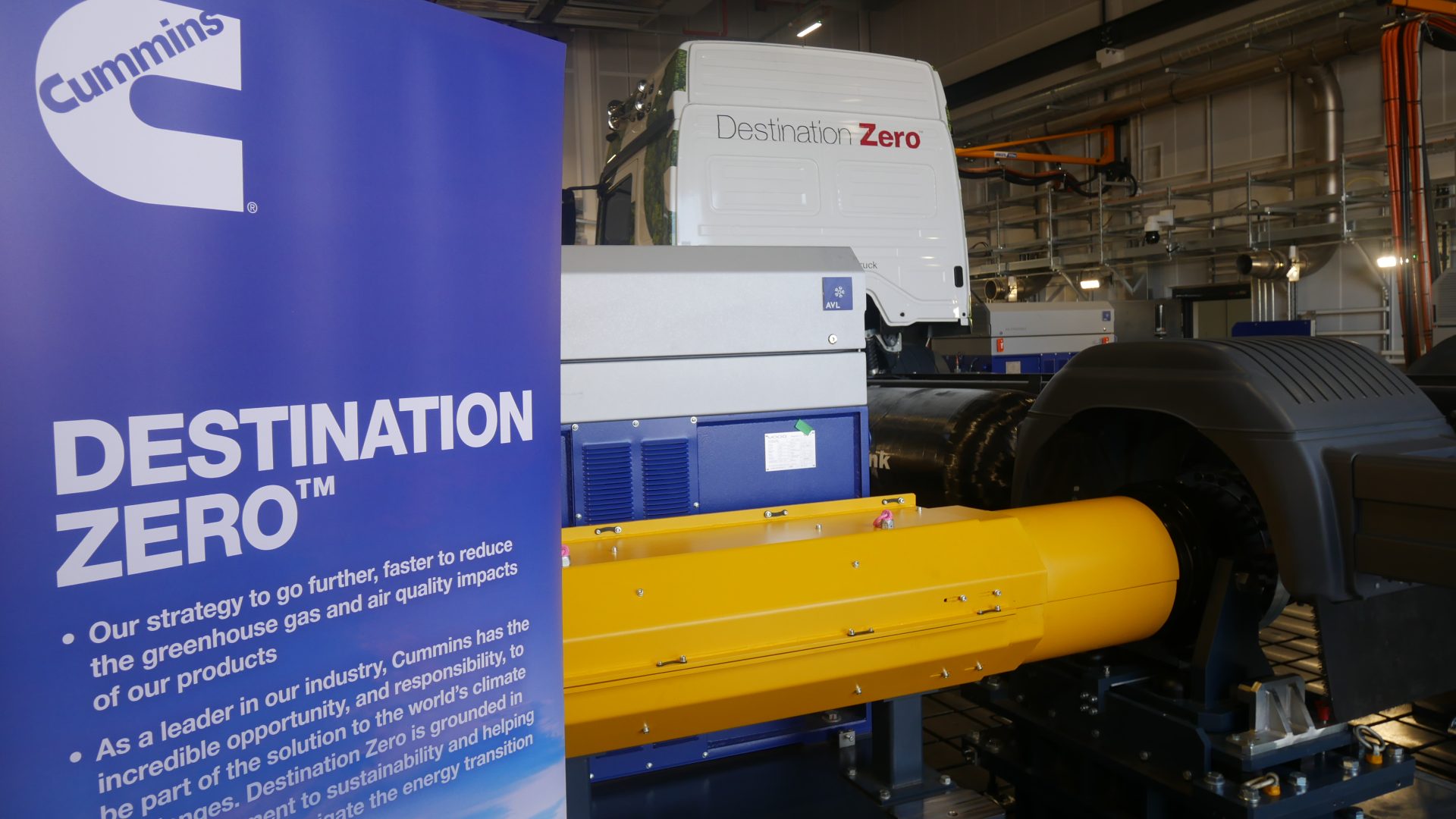
On-highway assets: the potential of the new facility
We return to Felipe Rocha for a global overview of Cummins’ on-highway assets, which are primarily the focus of the Darlington Powertrain Test Facility—a facility that is currently unique within the Cummins network. “In Europe, our business structure on the engine side involves major truck customers and partnerships with DAF, Scania, and Volvo,” Rocha says. “We also cater to bus customers in the UK and Turkey, covering a diverse range of midrange segments from 2.8 liters in Turkey to 9 liters. Recently, we announced a significant partnership with Daimler to develop Euro 7 engines for the mid-range sector, marking a major shift in our on-highway business. We are actively engaging in discussions with other OEMs as well. From my perspective, Cummins is pursuing a pragmatic strategy. We continue to invest in our traditional core technologies while simultaneously expanding and diversifying our product portfolio. We are committed to making new powertrains economically viable for users and providing a range of solutions. Cummins’ position is clear: we aim to support all equipment manufacturers facing the challenges of CO2 regulations. Whether it’s hybrid, hydrogen, or a combination of technologies, we offer various solutions for our customers to choose from”.