BorgWarner opens the doors to its Gigafactory in Darmstadt, now capable of producing 3.5 GW per year. Our report
BorgWarner welcomed us to its Gigafactory in Darmstadt. The plant can produce about 35,000 NMC battery packs in a year using innovative, highly automated lines. Investments in LFP batteries are planned to expand the company’s portfolio with products addressed to several sectors, from buses, to trucks, up to special vehicles. Here's what we saw in Germany.
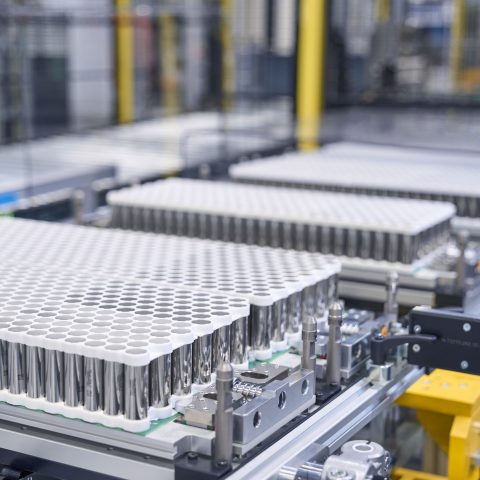
Where there was nothing before Covid, there is now one of the best-equipped gigafactories in Europe. The largest one excluding those belonging to OEMs. The acquisition, which was finalized in 2022, gave BorgWarner access to the battery production plants of former Akasol that now works on three shifts, five days a week using state-of-the-art, highly automated production lines.
In Darmstadt, not far from Frankfurt, production, testing area, offices and R&D occupy about 15,000 square meters, plus 4,000 square meters at the nearby Langen site. A total of more than 850 people are engaged in the design and manufacture of battery modules and packs, as well as BMS (Battery management systems) and Removable Contactor Box. In a nutshell, as of 2022 in Germany alone, BorgWarner’s battery systems division has produced about 5 GWh of battery packs for commercial and industrial vehicles using NMC (Nickel-manganese-cobalt) technology. This is set to increase significantly when the site’s maximum capacity of 3.5 GWh is reached, thanks in part to the finalization of a second highly automated production line. Considering also the other U.S. plant in South Carolina, the group expects a production capacity of about 5.4 GWh in 2025.
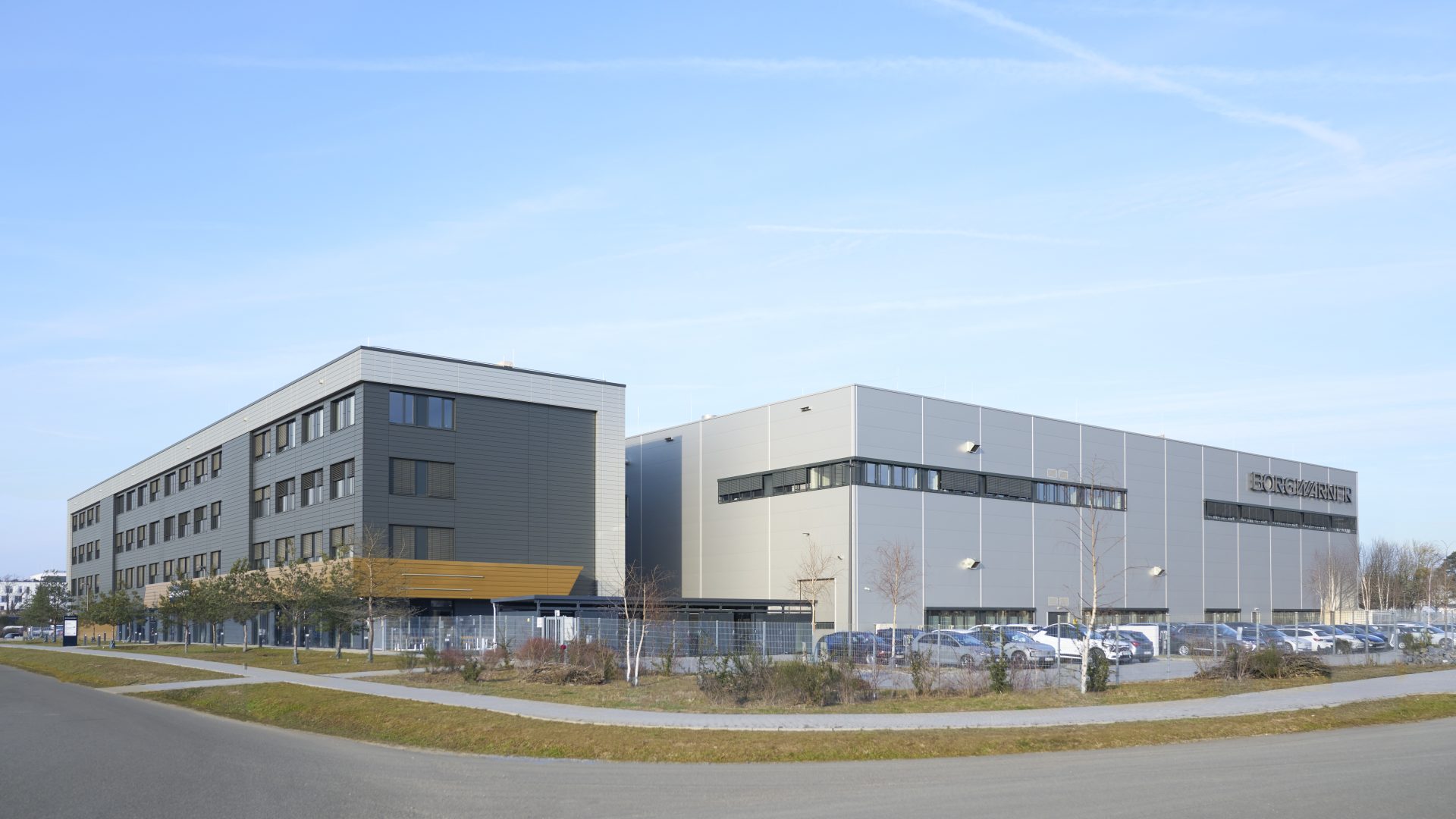
BorgWarner’s Gigafactory: module and pack assembly and testing
BorgWarner engineers showed us how the assembly lines work. It begins with the insertion of cylindrical cells inside the modules: the third-generation battery packs currently produced by BorgWarner admit two layers of 300 cells, for a total of 600 cells per module.
The processes of gluing (including preparing the cell surface) and adding the electronic connections – which are both entrusted to robots – is the most complex part. It takes more than one hours to manufacture a single module, which weighs about 50 kilograms, with an interval of a few minutes between the production of one module and the next.
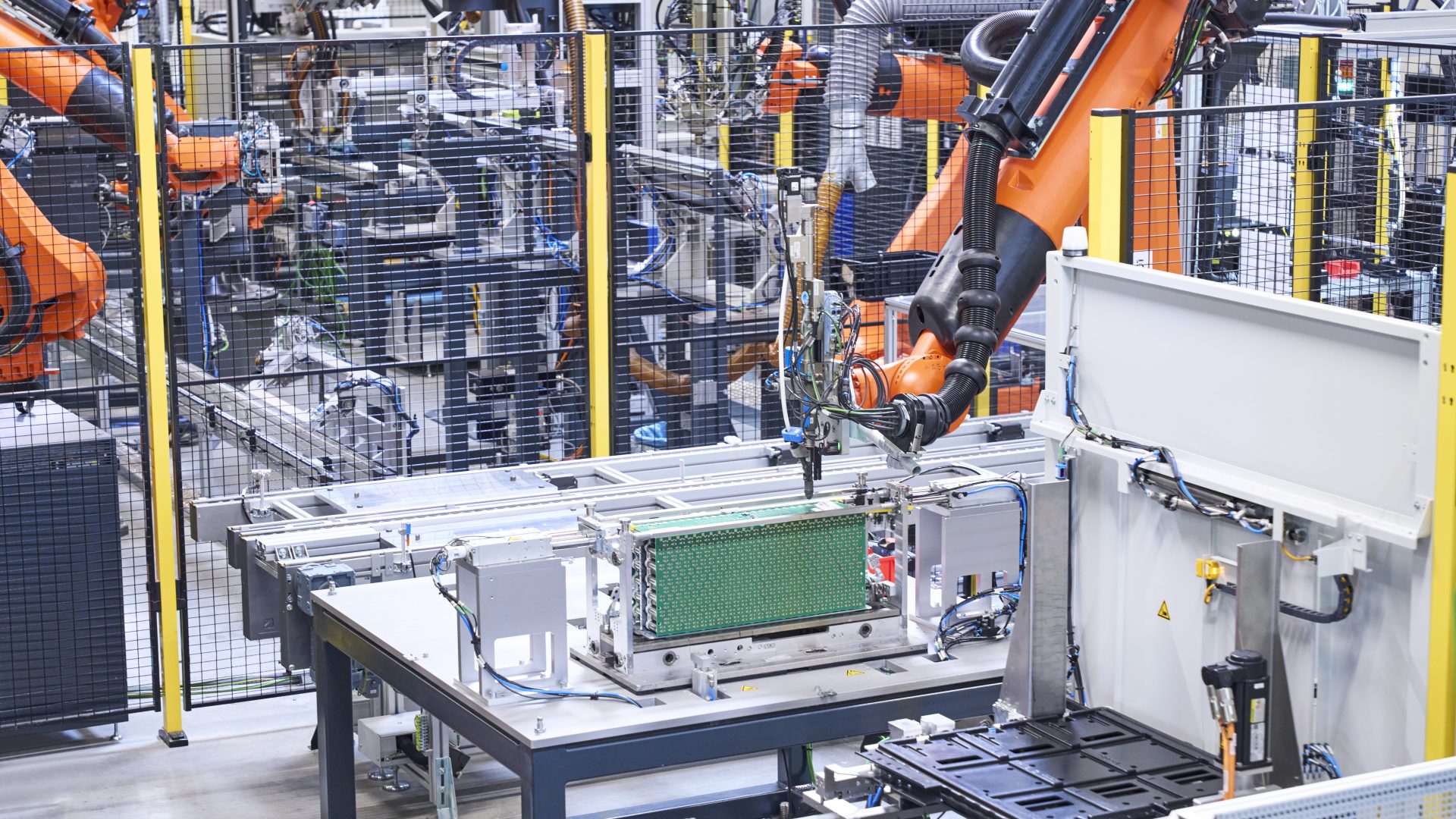
The production process of the battery packs, then the insertion of modules, is relatively simpler and is also entrusted to industrial robots for reliability and weight management issues. There are very few manual tasks overall, mainly feeding and operating the machines. Every around 20 minutes, the line makes a 9-module battery pack.
Potrebbe interessarti
Battery packs, EV chargers and portfolio resilience. Our interview with BorgWarner’s top management
Also, interesting and state-of-the-art is the testing area, next to production: slightly over 2,000 square meters where various types of tests (corrosion, immersion in water to monitor tightness, temperature, performance, vibration resistance, charge retention) are carried out on the battery packs, but also on the cells. These, although sourced from outside suppliers, are subjected to rigorous testing in controlled environments.
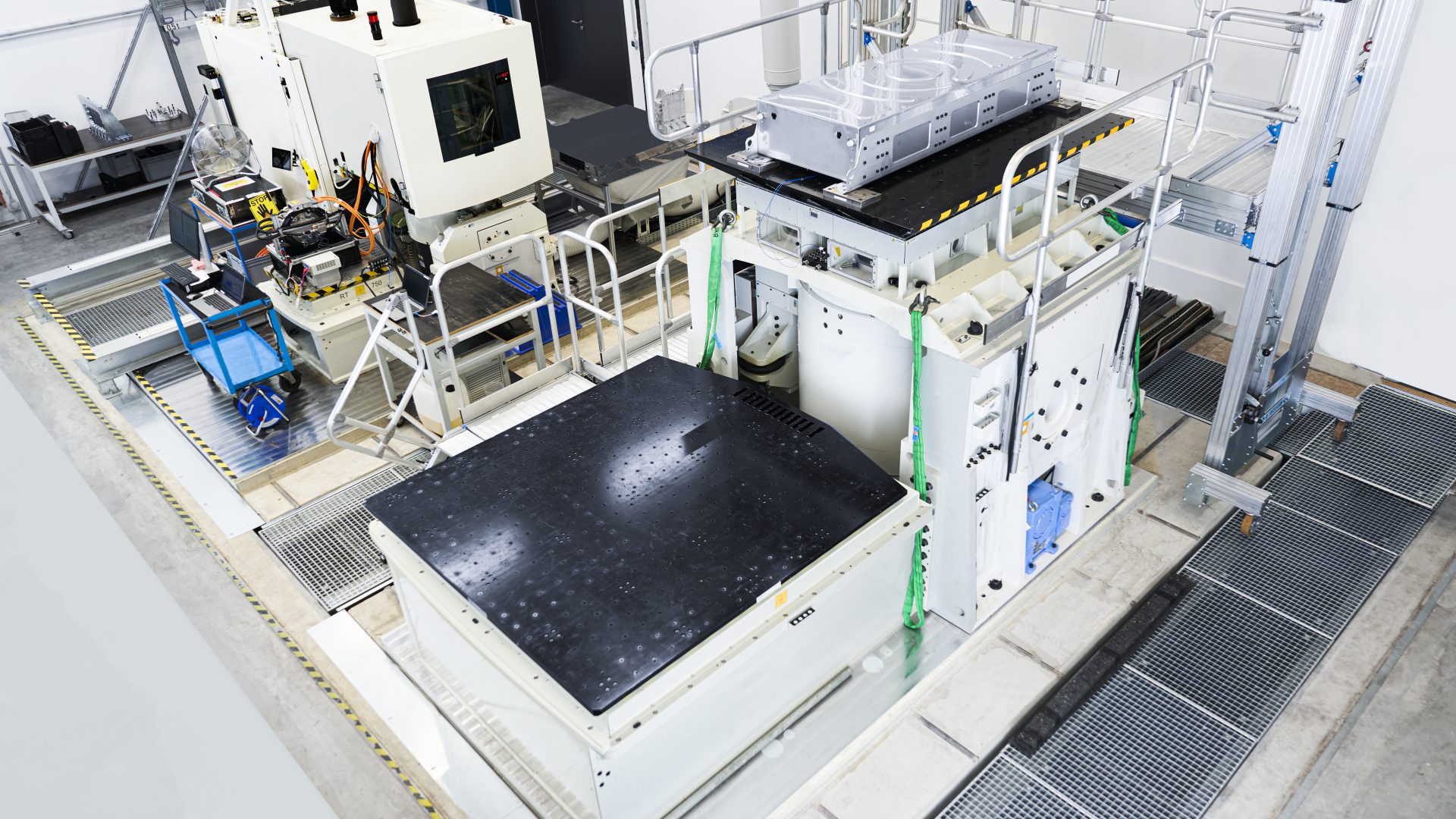
BorgWarner battery packs: the third generation and beyond
The third generation of UHE BorgWarner battery packs, i.e. those currently rolling off the Darmstadt lines, guarantee a capacity of 98 kWh with a nominal voltage of 665 V, continuous charging power of up to 80 kW, and a weight of just under 600 kg. A very important factor for the commercial and industrial vehicle sector is ensuring optimum operation over 4,000 charging cycles, a number that is far superior to car batteries. The company’s portfolio also includes a compact version with 5 or 6 modules instead of the standard 9. Trucks, buses, off-road vehicles (excavators, snow groomers, aerial platforms) and marine applications are the ones of choice for BorgWarner batteries, with the addition of projects in the field of eTrailers. So far, the bus sector has been very relevant: according to the American group, one in 5 e-buses in Europe and the U.S. mounts BorgWarner batteries.
What about trucks? The market, we know, is not flourishing, and at BorgWarner they are aware of that. However, they want to be ready when the numbers increase. And they are investing in new products, starting with LFP (Lithium-iron-phosphate) technology for cells: these will not replace the NMC ones produced today, but will be complementary, and the choice will be made based on the application. BorgWarner plans to diversify its offerings in terms of battery pack shape and size, with the obvious goal of meeting the construction needs of OEMs, especially buses and trucks (so far, LCVs are not a target for BorgWarner).
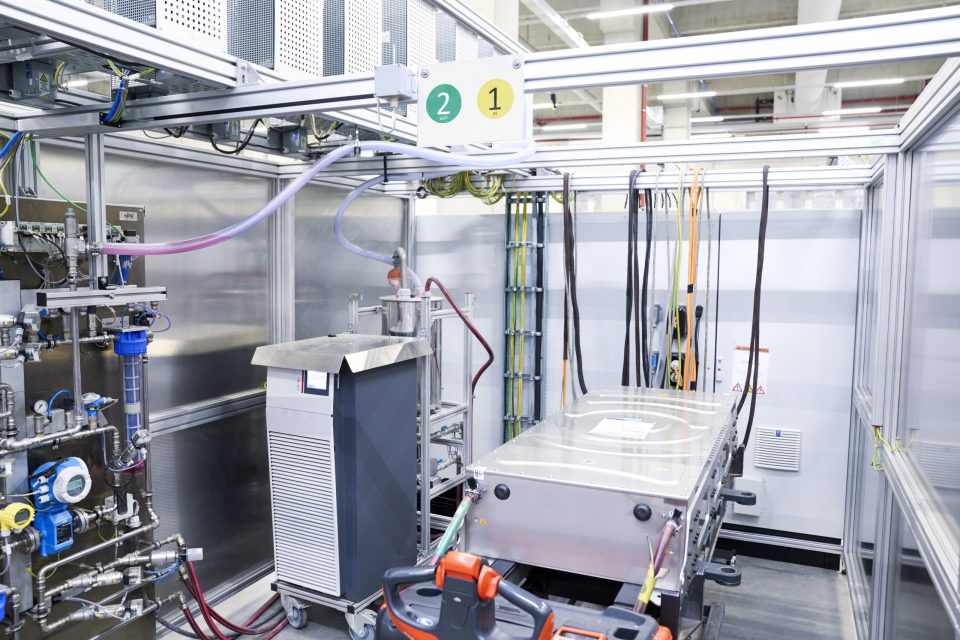
Looking, precisely, at the development of LFP batteries, the portfolio will consist of flat, high, compact or cubic products, without altering the hardware and software logic applied so far (such philosophy is called hardware and software foundation). Also, BorgWarner’s basic strategy will not change, at least for the next few years. The battery maker will continue to turn to trusted cell suppliers. Clearly, the FinDreams Battery partnership signed last year for the exclusive supply (outside China) of the innovative ‘blade cells’ goes in this direction. Thanks to an innovative and particularly compact design, these cells will provide manufacturers with higher flexibility.
A ‘win-win’ project, according to what’s been said in Darmstadt. Undoubtedly, the recent shake-ups in the young European battery industry give value to this choice.